WP1 – Hybridization
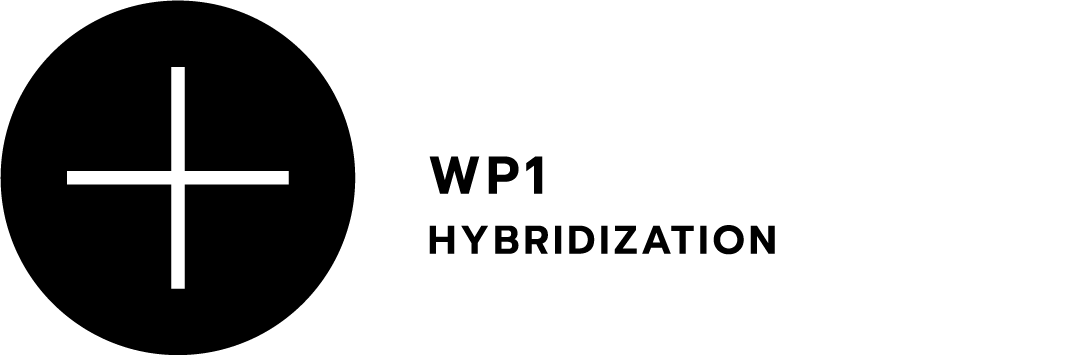
This project aims to introduce additive manufacturing in integrated production cells to enhance the technological conjunction in order to enable the industry to develop hybrid products in a sustainable and economical way, reducing time-to-market and simplifying the necessary steps, tools and equipment.
On a first approach, a product of the food sector will be analyzed, which may or may not have contact with foods, and which is typically manufactured using non-natural materials (e.g. petroleum) and conventional processes (e.g. injection molding). In this case, whenever one wants to obtain special series of customized products (e.g. the same product with different colors, shapes and logos) it is necessary to manufacture new molding inserts or even a new molding tool which may involve changes in production equipment (e.g. from 1k injection to 2k injection), therefore having a direct consequence on time-to-market, costs and energy expenditure, which are currently neither ecological nor beneficial for industries.
In order to mitigate the limitations that are inherent to this type of approach, the aim is to implement hybridization by integrating additive manufacturing in an integrated production cell, for the production of insert parts to be placed by automated means in a mold, ready for the next step of overinjection. Thus, one obtains a customized hybrid product without the need to change tools. The aim is also to integrate green materials into the product and, therefore, the development of bio-based materials (e.g. polylactic acid) with natural reinforcements (e.g. coffee, mussel by-products, cork) for additive manufacturing is to be expected. The conjunction of processes implies additional care in product design, considering the end of their life cycle.
As such, sustainable design strategies (eco-design) will be implemented to enable easier separation and recycling or reuse. This hybridization strategy for fast product customization, combined with sustainable materials and design, will ensure process and product efficiency and sustainability.
On a second approach, a product of the automotive sector will be analyzed, the process of which involving a product injection stage followed by a manual stage of application of a sealant. As it is manual, the latter varies in time and quality, with a high rate of rejection. The aim is to automate the process through hybridization strategies using additive manufacturing systems for controlled application of a sealant.
As such, a system for the extrusion/application of sealing material will be designed and manufactured such that it can be attached to a robotic arm system within an integrated production cell with on-site hybrid production and validation.