WP10 – PIMMach
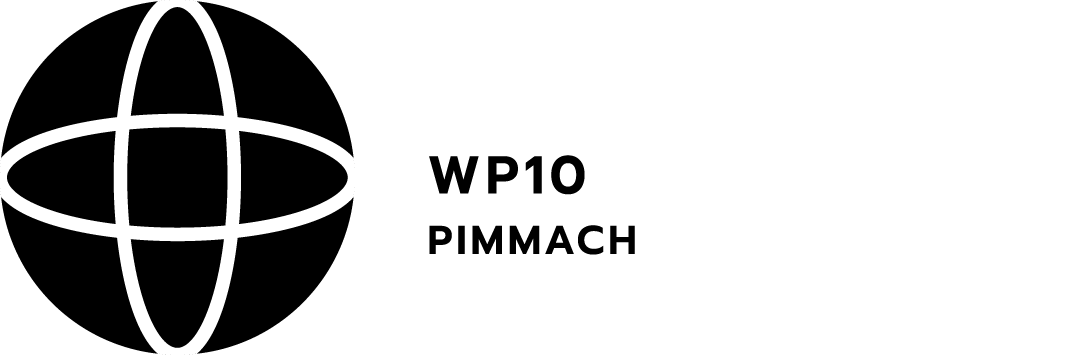
In an increasingly competitive global market, companies are focusing on the fast and effective development of new products to meet evolving demands and maintain competitiveness. The adoption of additive manufacturing (AM) processes and materials, particularly those that are complex to process, exemplifies this strategic adaptation.
Within this development scope, creating highly complex and optimized geometries offers a significant opportunity to advance materials suited to AM processes, enabling the construction of intricate components that maintain high-quality and cost-efficient standards.
Metallic component production can be achieved through either subtractive or additive processes. Subtractive methods are generally time-intensive, involving multiple steps and equipment, making them less suitable for components with high geometric complexity. Conversely, metal-processing additive manufacturing enables the construction of highly complex shapes, although it typically requires specific material properties and entails high energy consumption due to the use of lasers or energy-deposition technologies over powder beds.
To curb energy costs and enhance production speed, extrusion processes for metallic materials are being explored, drawing from injection techniques that use metallic materials within polymeric matrices.
This project addresses the demand for complex metallic components (such as plastic molds and glass) through additive and hybrid manufacturing techniques based on extrusion and machining. An additional goal is to develop the necessary raw materials using PIMMach-based processes.
The entire system will be integrated within a work cell, using anthropomorphic robot systems to transfer products between devices in the cell. This project will not only respond to specific industry needs but will also create new market opportunities at both national and international levels. Key challenges for the project include:
- Machining components in a green state to improve precision and minimize final processing time.
- Software integration to streamline operations across devices within the work cell.
- Software development for deposition paths, optimising material placement and geometry for each component.