WP11 – Selective.Powder
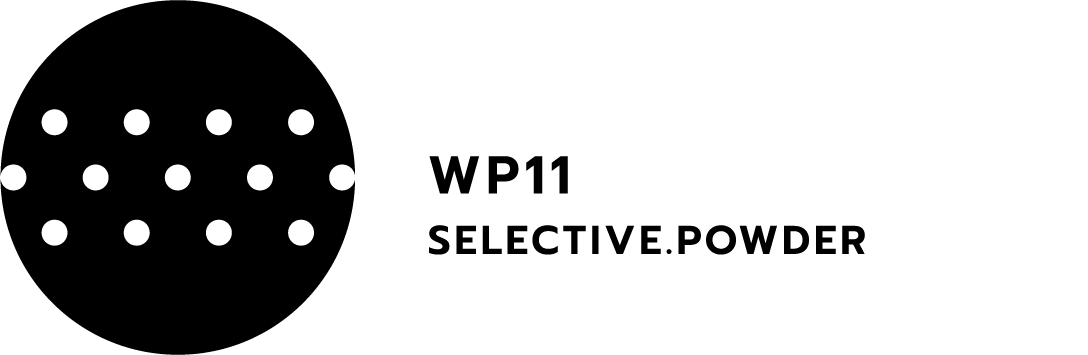
Additive manufacturing (AM) processes, capable of processing metals, allow for the construction of highly complex components. However, their fabrication requires very specific material properties and high energy consumption, as most processes used in industry involve lasers or energy deposition nozzles over a powder bed.
In order to reduce energy consumption and speed up the production process, research has been focused on metal powder deposition processes that can be sintered to obtain a final product with high detail and complexity.This approach aims to address current needs in the production of complex metal components (such as plastic and glass molds), using metal powder deposition techniques.
After depositing of the metal powders (in high temperature resistant crucibles), they will be sintered in a furnace, under inert gas atmospheres. Once sintered, the result will be finished parts with controlled surface roughness and complex internal geometries
The goal is the development, implementation, and operational application of a selective powder deposition system, specifically designed for the production of metal components. This system consists of a selective material deposition unit and a sintering furnace with an inert or inert-gas-purged atmosphere, using argon or nitrogen.Application tests will be carried out on injection molds.
As a sustainability strategy, the use of powdered silica as a support material will be explored. This powder has a higher sintering temperature than the materials used, allowing it to be reused in the production of new parts — supporting a circular economy approach.