WP12 – MoldPrint.XL
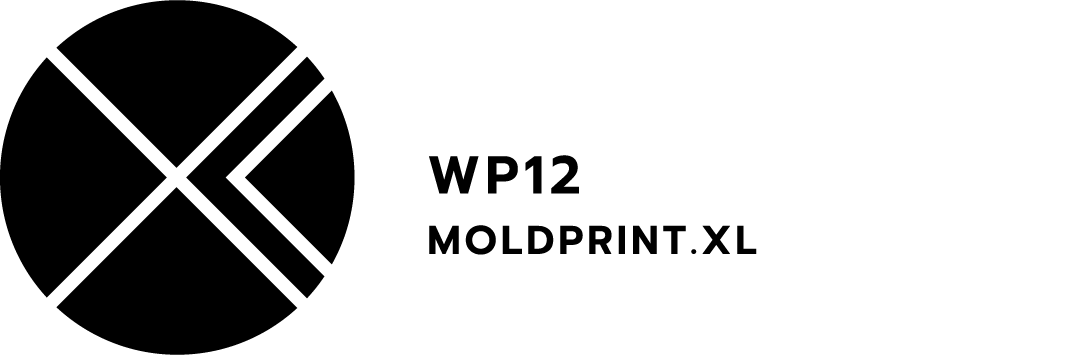
The development of additive manufacturing (AM) technologies has been a major focus in recent decades, with further growth anticipated in the years ahead. This expansion is driven by the continuous need to reduce cycle times, increase product customization, and address sustainability in product development. Together, these factors enhance time-to-market, boosting profit potential and enabling companies to stay competitive in their markets.
However, AM technologies still face challenges, particularly concerning the viability of substantially large parts. Key issues include construction time, surface finish, and reduced efficiency in large-quantity production.
In the maritime mobility sector, mold production currently relies on conventional technologies, which typically require weeks or even months due to the large scale involved. Once a mold is complete, the product manufacturing process begins, extending the overall production time.
To tackle these challenges, large-scale additive manufacturing systems are being developed for use in direct component construction and large mold manufacturing, meeting the demands of composite material molding processes.
This project aims to develop and implement a complete additive manufacturing system with a build area of up to 12 meters, capable of processing both thermoplastics and thermosets through extrusion. This capability will allow for the production of near-final dimension parts, which can be subsequently machined to desired specifications. Additionally, the project emphasizes circular economy principles, ensuring that the developed products are recyclable at the end of their lifecycle.
The project’s value lies in advancing innovative and sustainable AM techniques for thermoplastics and thermosets, facilitating the creation of high-quality molds and products that align with current industry needs.