WP13 – LAAM.Composite
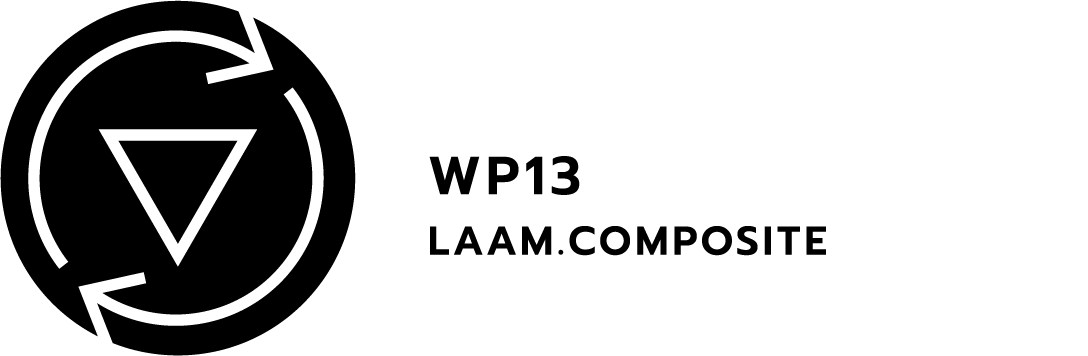
Manufacturing large-sized composite material parts presents challenges in both design and production when using traditional methods. This project addresses key obstacles in the following areas:
a) High Cost of Molds: Conventional methods for producing large composite parts typically require molds, an expense that is prohibitive for small production runs. These molds, generally made of metal, are created by machining large material blocks to achieve the desired surface. Additive manufacturing (AM) offers a solution through its versatility and flexibility, allowing various geometries to be manufactured with minimal material usage and reduced machining requirements.
b) Recycling Challenges for Composites: The reuse of composite materials poses a major problem for current recycling methods. Without viable solutions, these materials often end up in landfills or are incinerated for energy recovery. This project aims to facilitate an ecological transition by integrating recycling units capable of reclaiming end-of-life composite fibers and reintegrating them into the production of new parts through additive manufacturing.
c) Dimensional Accuracy in Additive Manufacturing: AM processes may lead to dimensional inaccuracies in finished parts, causing incompatibility with final applications. This project seeks to develop monitoring strategies and closed-loop control systems to manage these deviations. Such systems analyze real-time deviations in comparison to the intended part geometry, adjusting the deposition process to meet required specifications and producing viable final geometries.
d) Support Material Reduction: Thermoplastic/composite deposition processes require high amounts of support material, a challenge especially for large-area additive manufacturing (LAAM). This project proposes the development of a pinbed forming system with independent actuators, allowing printing on non-planar surfaces. By adapting to the part’s geometry along the vertical axis, this solution reduces the need for supports in overhang geometries.
e) Mechanical Properties for High-Load Applications: Current thermoplastic and short-fiber composite deposition methods do not provide adequate mechanical properties for parts subjected to heavy loads. To address this, the project will develop a deposition head for continuous fibers, enabling the production of high-performance components with enhanced mechanical properties. This method allows for thinner parts with better performance compared to short-fiber or purely thermoplastic alternatives.