WP2 – Hybrid Molds for Polymeric Products
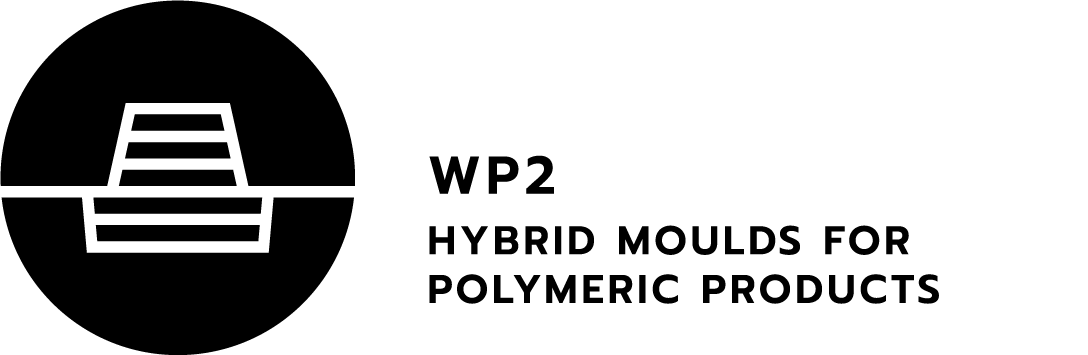
The idea of this project is to create a productive tool from the combination of different technologies and materials, with the aim of obtaining polymeric parts for everyday use.
This tool is called a hybrid mold because it consists of a conventional structure and molding inserts that are produced by combining traditional and additive manufacturing materials, through both conventional and additive manufacturing technologies.
The hybrid mold can be used as a molding tool, e.g., in injection molding, thermoforming, blow molding, and other technologies, for the production of small to medium series, as well as to make injected prototypes for product or system validation before large-scale production. With hybrid molds, there is the possibility of embracing new markets, such as the production of small customized series, replacement parts, and test parts, to accelerate product development. Based on this idea, product 1 will be developed, consisting of a hybrid mold with molding inserts for the production of polymeric parts through the process of injection molding.
Hybrid molds with molding inserts produced through additive manufacturing (AM) present some challenges, including: low durability of the inserts; scarce availability of AM polymeric materials with the necessary characteristics; low heat transfer from existing polymeric materials; probability of adhesion between the materials to be injected and the molding inserts (when produced with polymeric materials); poor surface quality (depending on the AM technology); inaccurate dimensional tolerance; the impossibility of placing channels in the molding inserts (when produced with polymeric materials) for thermal control; and limitations in the injection of parts with complex geometries.
To address some of these challenges in injection molding inserts produced through AM, the objective is to study different cases, such as polymeric parts with thin, transparent walls and areas that require metallic pieces in the molding insert. Additionally, there is a plan to develop product 2, based on a new coating suitable for additively manufactured polymeric materials, to be applied to product 1. This new coating will improve the performance of hybrid molds and address some of the identified issues. The application of this coating will enhance the surface quality of the molding inserts produced by additive manufacturing and reduce the adhesion between the material of the molding inserts (when polymeric) and the material to be injected, making it easier to extract the injected polymeric parts.
At the end of the process, the hybrid mold will be validated, facilitating the development of polymeric products with complex geometry for the automotive industry, through the application of surface coatings and/or metallic pieces in the molding inserts.