WP24 – Molding Inserts for Parts with Micro-Details
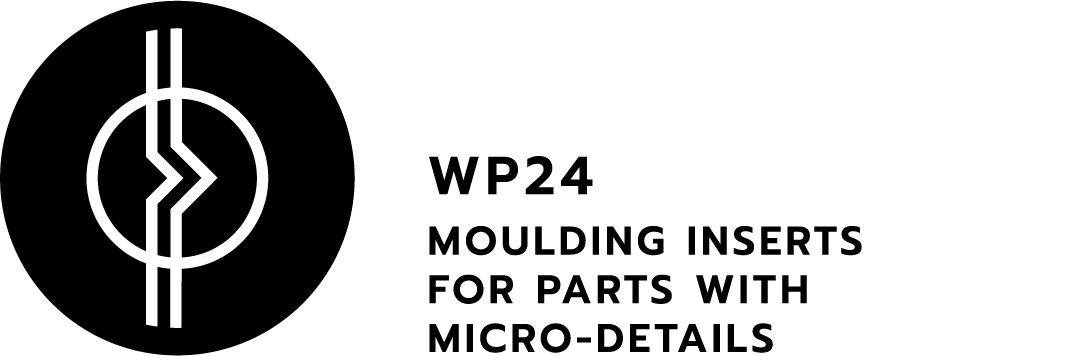
Additive Manufacturing (AM) technologies are mainly used in fast prototyping, but their evolution has led to their application in the production of final parts, making AM a leader across several markets. These technologies rely on a layer-by-layer manufacturing process based on 3D CAD models, adding material in various formats and types.
In injection molding, AM is primarily used for producing molding inserts, allowing geometric details to be replicated with high accuracy and enabling conformable cooling channels. This technology can achieve final product quality comparable to traditional metal machining methods, with the added benefits of producing inserts in under 24 hours and minimizing material waste.
Additive manufacturing techniques make it possible to model and develop complex geometries within the mold design that would be unachievable using conventional material subtraction processes. Consequently, metal inserts in molds with intricate structures can be designed with optimized cooling channels, significantly reducing injection cycle times.
This approach represents substantial progress in tool production efficiency, optimizing raw material use and reducing energy consumption. The inclusion of conformable cooling channels, achievable only through AM, allows channel designs that closely follow the part’s entire geometry. Another benefit of this new approach is the ability to produce inserts with superior surface finish and geometric precision, accurate to the micrometer scale.
The project includes developing a methodology for structure optimization, covering sizing, simulation, validation, and real testing. Molding inserts are developed through a process utilizing structural and thermal mold simulation software, maximizing the advantages of these technologies and minimizing their impact on final production quality.
The use of design software will also be essential for sizing and modeling all components for manufacturing. The entire lifecycle of metal inserts with micro details, from production through additive manufacturing to their performance as a productive tool, will undergo comparative life cycle analysis against standard tools currently in use.