WP3 – Hybrid Molds for High Performance Products
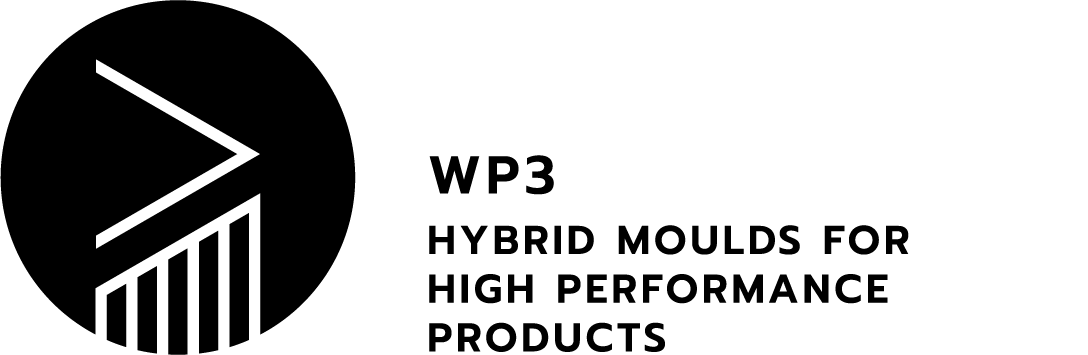
Technology is constantly evolving, always requiring new components to keep up with market developments. The injection molding process has been one of the most widely used methods in recent decades to produce plastic parts for everyday items such as communication devices, electronics, kitchen appliances, and consumer products.
The main objective of this Work Package (WP) is to develop productive tools that result from the combination of different technologies and materials, with the aim of obtaining polymeric parts by injection for everyday use. These tools are called hybrid molds, as they consist of a conventional structure and molding inserts produced by combining traditional and additive manufacturing materials, through both conventional and additive manufacturing technologies. The hybrid mold can be used as a molding tool in injection, thermoforming, blow molding, or other technologies for producing small and medium runs, as well as for creating injected prototypes for product or system validation before mass production.
With hybrid molds, there is also the potential to tap into new markets, such as small customized batches, production of replacement parts, and test parts for accelerated product development.
The project will develop a product consisting of a hybrid mold with molding inserts for producing high-performance polymeric parts through the injection molding process, specifically for the heaters, boilers, and heat pumps industry.
The aim of hybrid molds is to reduce the time-to-market and the cost of small production runs. Key advantages of hybrid molds include efficiency in terms of reduced waste and energy consumption and the ease of customizing channel layouts in temperature control systems. One of the main benefits of hybrid molding is the ability to design temperature control systems with conformable channels that match the part geometry.
The primary objectives of this WP are:
- Develop at least one high-performance polymeric product using hybrid molds;
- Study different materials, technologies, and geometries for the development and production of molding inserts;
- Use conformable channels to effectively conduct heat from injection into molding inserts;
- Reduce the final cost of the product;
- Minimize time-to-market from development to product availability without compromising quality;
- Evaluate the economic and environmental impact of the high-performance polymeric product and its respective hybrid mold.