WP4 – MOLD5G
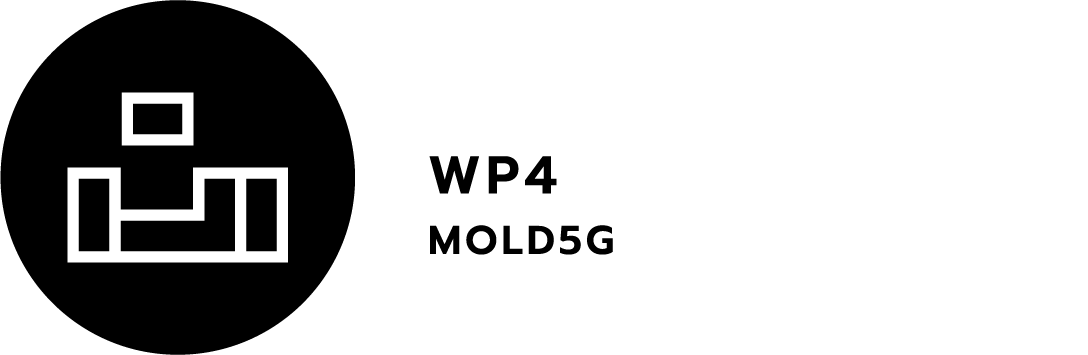
In the injection molding sector, additive manufacturing is predominantly used in producing molding inserts (components that give the product its shape), which are made from various materials such as polymers and metal. The additive manufacturing technology at the foundation of this project is metallic sintering in a powder layer. This technology offers quality comparable to current machining processes but has advantages in production times, material waste reduction, and process versatility, including the ability to repair molding tools.
Using additive manufacturing as a manufacturing process for the molding tool marks a significant step in optimizing raw material resources. However, to achieve substantial and sustainable optimization, it is essential to design a complete molding tool tailored for additive manufacturing.
This approach provides greater freedom in optimizing material resources for tool production. For example, it reduces the energy required during production by optimizing the tool’s weight to use only what is necessary, as opposed to traditional processes. Additionally, it minimizes the number of tool components, reducing assembly times and improving performance, and offers unconventional techniques like conformal channels. These channels, only possible through additive manufacturing, allow for non-standard geometries.
A unique aspect of this advanced molding tool design is the incorporation of process monitoring sensors (e.g., pressure and temperature sensors). These sensors make the molding tool an intelligent product, providing real-time feedback on the process state and highlighting parameters that can be optimized. Additionally, the tool sends feedback to the manufacturer, enabling preventive maintenance and adjustments.
Developing the molding tool will involve specialized design software for additive manufacturing, such as generative design and topological optimization software, which optimizes material mass based on expected performance. This approach maximizes the benefits of additive technologies while minimizing their impact on final production.
Structural and thermal simulation software will also be utilized to evaluate and validate the tool’s mechanical and thermal performance, along with injection process prediction software. The integration of these elements is crucial for validating the tool within a digital environment.
The molding tool design will incorporate standard components to ensure compatibility with existing injection molding machines, allowing seamless tool utilization without needing machine adaptation.